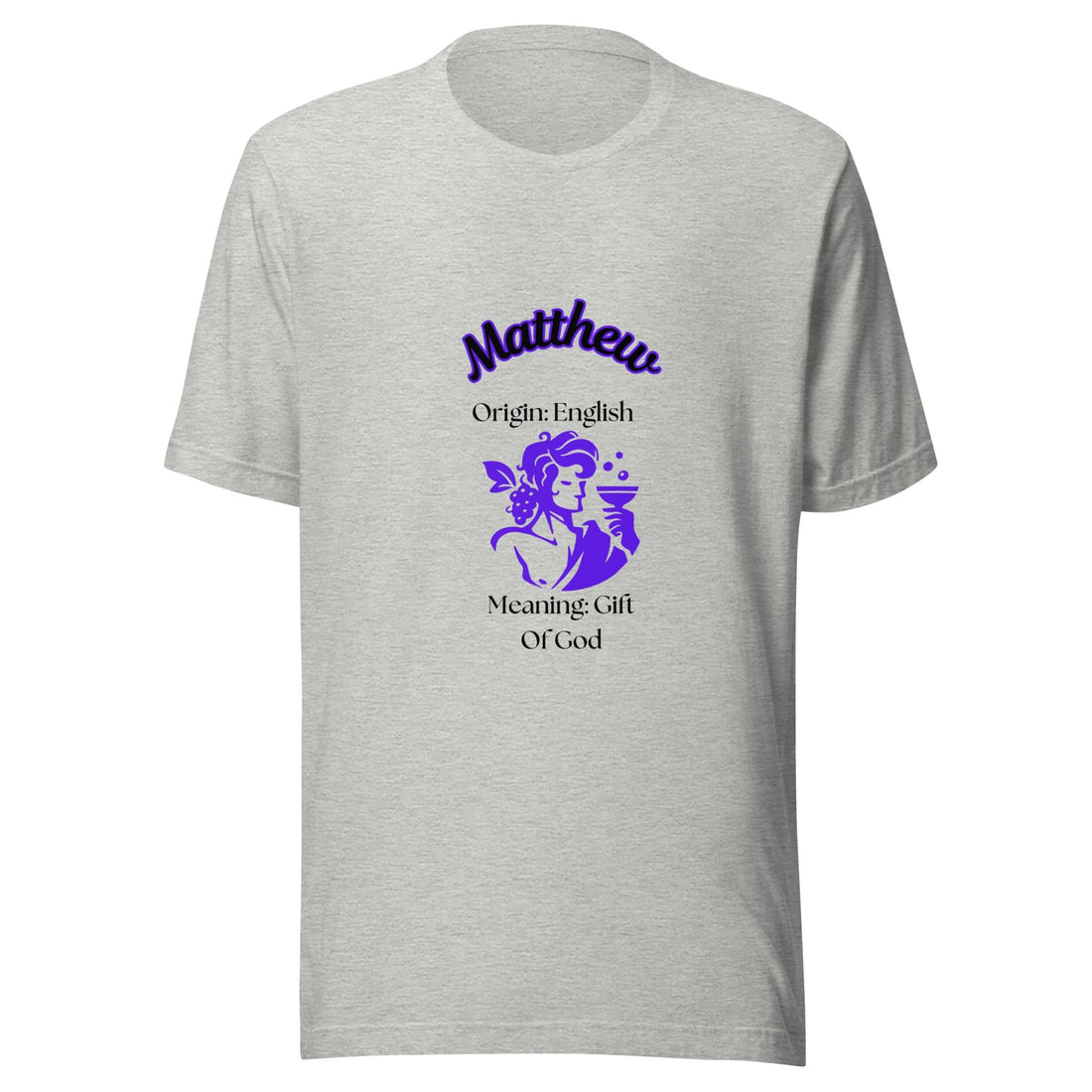
How T-Shirts Are Printed: A Behind-the-Scenes Look at Your Favorite Tees
Compartir
Ever wondered how your favorite graphic T-shirt goes from a blank piece of fabric to a wearable work of art? Whether it’s a clever slogan, a cartoon character, or a custom design you uploaded online, there’s a fascinating process behind getting that image onto a shirt. In this article, we’ll explore the most popular T-shirt printing methods, the materials involved, and the steps it takes to bring those stylish threads to life.
The Basics of T-Shirt Printing
T-shirt printing refers to the process of applying ink, dye, or heat-transfer material onto a fabric surface—typically cotton, polyester, or blends. The choice of printing method depends on factors like quantity, design complexity, budget, and turnaround time. Some techniques are better for bold colors and high-volume orders, while others are ideal for small batches and detailed artwork.
Let’s break down the most common T-shirt printing techniques.
1. Screen Printing (Silkscreen Printing)
Screen printing is one of the oldest and most popular methods of T-shirt printing. It's widely used for bulk orders and known for producing vibrant, durable prints.
How it works:
A mesh screen is created for each color in the design. Ink is pushed through the screen using a squeegee onto the fabric below. Once printed, the shirt goes through a dryer to cure the ink.
Pros:
-
Long-lasting prints
-
Cost-effective for large runs
-
Excellent color vibrancy
Cons:
-
Not economical for small quantities
-
Limited to a few colors per design
-
Setup can be time-consuming
2. Direct-to-Garment (DTG) Printing
Think of DTG printing like using a giant inkjet printer—except instead of paper, it prints directly onto fabric.
How it works:
DTG printers spray water-based ink directly onto the T-shirt. The design is first pre-treated, printed, and then heat-cured to set the ink into the fibers of the shirt.
Pros:
-
Ideal for complex, full-color designs
-
Great for small batches or one-offs
-
Soft, breathable print feel
Cons:
-
Slower than screen printing
-
Works best on 100% cotton
-
May fade over time with heavy washing
3. Heat Transfer Printing
Heat transfer uses heat and pressure to apply designs onto T-shirts, typically with vinyl or transfer paper.
How it works:
A design is printed on special transfer material using solvent ink or cut from vinyl. It’s then pressed onto the shirt using a heat press machine.
Pros:
-
Great for customizing names/numbers
-
Vibrant results with fine detail
-
Lower setup cost
Cons:
-
Can feel thick or rubbery on the shirt
-
May crack or peel over time
-
Not ideal for high-volume production
4. Sublimation Printing
Sublimation is a favorite for all-over designs, especially on polyester shirts.
How it works:
Sublimation dye is printed onto special paper and then transferred to the T-shirt using heat. The heat turns the dye into gas, bonding it directly with the fabric fibers.
Pros:
-
Seamless, all-over designs
-
No cracking or fading
-
Great for performance and sportswear
Cons:
-
Only works on polyester or light-colored garments
-
Not suitable for cotton
Steps in the T-Shirt Printing Process
No matter which method is used, T-shirt printing generally follows these core steps:
-
Design Creation: Using software like Adobe Illustrator or Canva, the artwork is prepared in the correct format.
-
Preparation: Screens are made (for screen printing), or shirts are pre-treated (for DTG).
-
Printing: The design is transferred to the shirt using the selected method.
-
Curing: Ink is set using heat to ensure durability.
-
Quality Check: Shirts are inspected for alignment, color accuracy, and flaws.
-
Packaging: Finished products are folded, bagged, and shipped or stored.
Which Printing Method is Best?
It all depends on your needs:
-
Need 500 shirts for an event? Go with screen printing.
-
Selling detailed artwork on-demand? Try DTG printing.
-
Customizing team uniforms? Heat transfer might be your best bet.
-
Want a full-shirt, all-over pattern? Sublimation is the way to go.